Tandem’s Telstra excavation permit survey and review process
Paul Donker
Executive General Manager – Health, Safety & Environment
Tandem Corporation
The role
I’m the Executive General Manager for Health, Safety and Environment for the Tandem group of companies, where we manage installation and maintenance, medium construction and civil construction. I’ve been at Tandem for about seven years, and prior to that I had a background with a number of other large organisations, including NBN. So, telco is a large part of my career.
My portfolio is essentially health, safety and environment and the quality of our management systems across Tandem, from strategic direction through to risk management, and then our assurance programs including field based monitoring to make sure that those systems are effective across the Tandem group of companies.
The role of technology
Technology enables us to embed business rules, requirements, standards and processes into our system which then forces those outcomes to happen. Technology is an enabler of assurance. Without actually having to get to a site, we can use technology to increase our scope and coverage of those assurance activities without actually having to throw additional resources at it. The technology captures real time artefacts and then enables us to remotely validate those artefacts.
The field services applications we use, capture detailed artefact information to enable trend analysis, identifying issues before they arise. Part of our strategic direction is to continue to leverage systems to use more remote monitoring capability, so we can increase monitoring validation in real time. Technology embeds the business rules that we need and supports people to follow a process.
Technology drives efficiencies
Efficiency means doing more with less, so rather than sending a person to manage an assurance activity at a site, I can do more using technology to do that for us, and by building business rules into the technology, so you can’t start the next part of the process until you collect the relevant artefacts. The system either interrogates or checks progress. Or it’s checked remotely. I don’t need to send a person to a site, I can have a person remotely check the submitted activities. We can just get people to go ahead to do those tasks, doing much more with less.
The business problem
We implemented a best-practice process based on our safety requirements. The challenge was to build a process that has two validation points. First, a validation of the underground assets and whether the planned excavation is deemed either low, high or extreme risk. We check what assets are in the ground and then based on that, determine what permit needs to be completed at site. We engage a team to check or validate that we’ve made the right determination about what needs to happen at the site.
For the second validation point where we have identified high or extreme risk assets we will need to work near, we have an on-site review involving a team member to make sure the civil crews are completing the task in adherence with all safety processes.
We’re focusing on the first validation point now, making the right determination. So, you can’t move to the next stage until the system and the business rules within the system are approving this first stage or this first validation point.
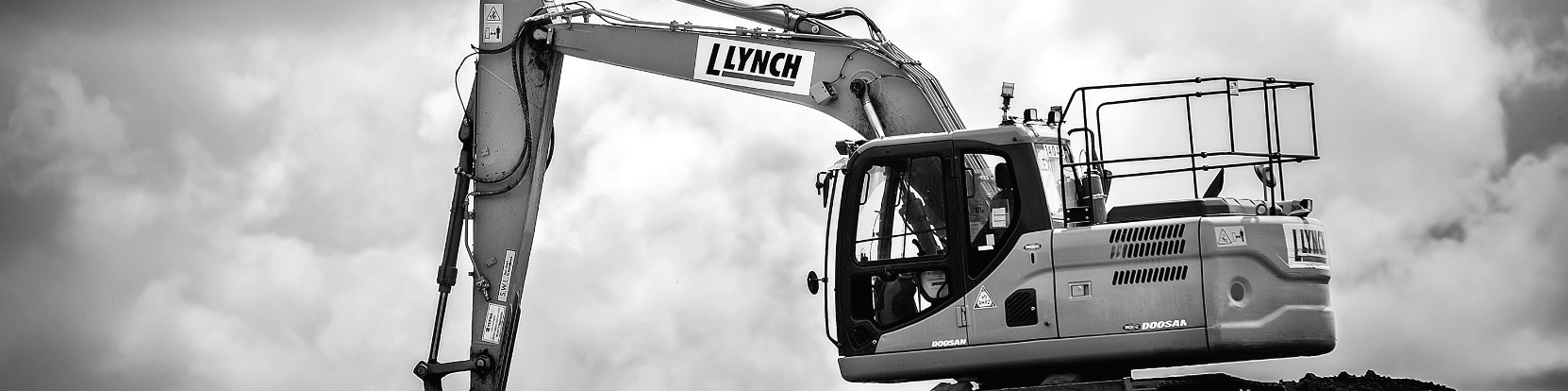
Safety as a client directive
We put a process in place at the request of our clients to manage their construction. Once we implemented it and looked at it over one or two months, we identified an opportunity to use a system change to provide process assurance. The customer requested a system change, or a change in the process, to provide a hold point. The purpose of the hold point was to prevent the work from happening in the field until a validation of that hold point has been completed. And I would see that as absolute best business practice. It’s probably going a bit above and beyond. Many organisations rely on people to do the right thing. This essentially takes that decision-making process away and makes sure that work in the field cannot even commence until this additional safety check has happened.
The challenges to address now
We have a number of stakeholders in the process , including clients, Tandem, and Tandem subcontractors. The challenge was to deliver an automated system that reduced effort, created a single point of truth, prevented field work from commencing without safety checks occurring, with all these automated and monitored from a system/field perspective, using system enforced hold points.
Implementing the change
Our project planning was well organised with weekly meetings and updates. From experience, I’ve always said that having dealt with a number of IT solutions over my career, you’ve usually got to double the time and double the cost. In this case we actually stuck to the timelines. and the cost was almost unchanged. So, that’s a really good outcome for Tandem and for Yarris, who scoped the system build well and held to the agreed project plan.
The weekly meetings involved a large stakeholder audience, including Telstra, operational management, heath and safety and, work deployment (very much part of the process) and those how were interacting with our sub-contractors to get feedback also.
It was good to open it up to a wider project team to gain input from all stakeholders. Where issues arose, we received feedback quickly about whether we could accept it or not, or suggest slight modifications to the plan. I saw a really quick response from Yarris on that one. And there was good feedback from Yarris – in real time.
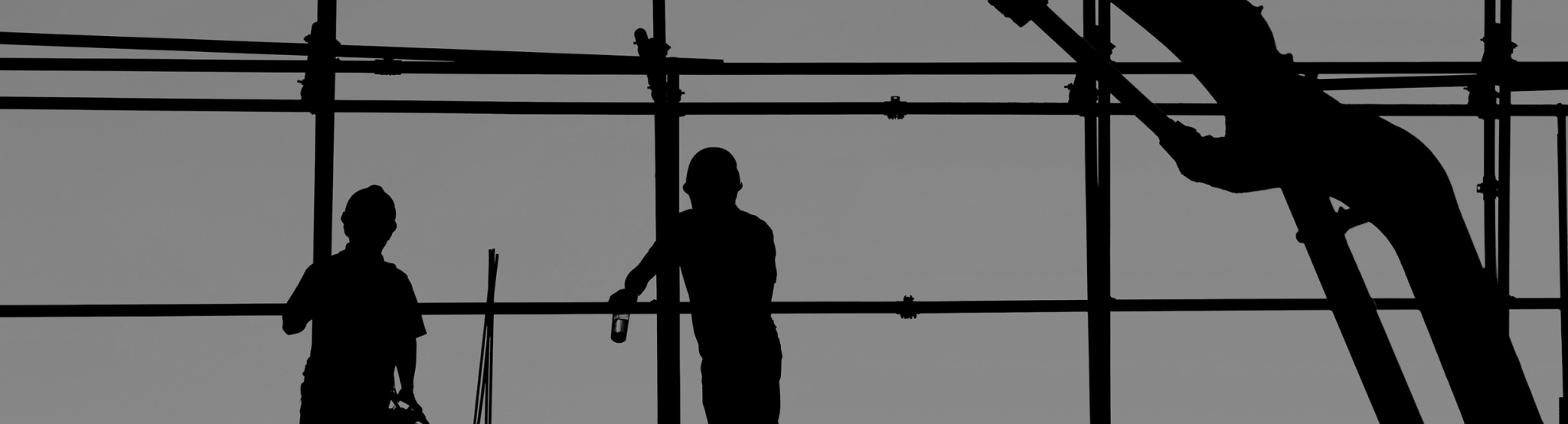
The outcomes
When we submitted the scope, it was quite open. Essentially, ConSol had some of the functionality we required and process support we were trying to achieve. I actually liked the way that the ConSol team designed the solution, using as much existing functionality within the system as possible, so they weren’t recreating the system. As the workshops developed, and as we met, week after week, developing the simplicity in the screens together was really good.
There’s an incredible amount that happens behind the scenes. And when I looked at the process, that actually, to me, was a very simple process, create this hold point one, require the subcontractors, to do this, tick this box, tick that box. Yarris made it simple in and intuitive for users , a good outcome for the people using the system.
Our users know they need to tick this box or upload this document, they don’t need to know what sits in the back end about all the business rules working behind the scenes. It means if they do the wrong thing, it won’t let them get to the next state. That’s what the ConSol team brought – simplicity from a user perspective. So, all those business rules that are happening in the back end, which we sorted out through a lot of questions, you’ve taken all that work, and made an appealing system – really simple and intuitive. It was great that the feedback from subcontractors around the user acceptance testing confirmed that it was going to reduce their admin time.
Subcontractors could instantly see the benefits of using this system, rather than a manual process relying on emails, which may get lost. This automates the process and gets rid of all that lost data. Putting an end to re-keying the same data twice. With the data already in the system, they see or reuse it. . There are dropdown boxes to speed up their process. Great to see that initial feedback from them.
What’s next?
For our hold point functionality we created a very detailed process flow from an end-to-end perspective of excavation works and having a low, high or extreme risk permit approved. Hold point one is the risk assessment of which permit needs to occur.
And then we’ve got hold point two, which we’ll look at next with another project to capture video and artefacts from hold point two and automate these back into ConSol. We’ll see if we can create some system smarts within ConSol, that can help us with hold point two.
We also want to tackle multiple-channel video calls, where we have to call in a number of different stakeholders to approve that permit on site. So, whether we go to site or not, we’ve still got a process where we have to have video/photos records so there’s a good artifact evidence.
I think there’s still an opportunity to further automate some of these processes within ConSol to further improve the system to ensure greater efficiency and assurance. I hope we can collaborate on that once we wrap this one up.
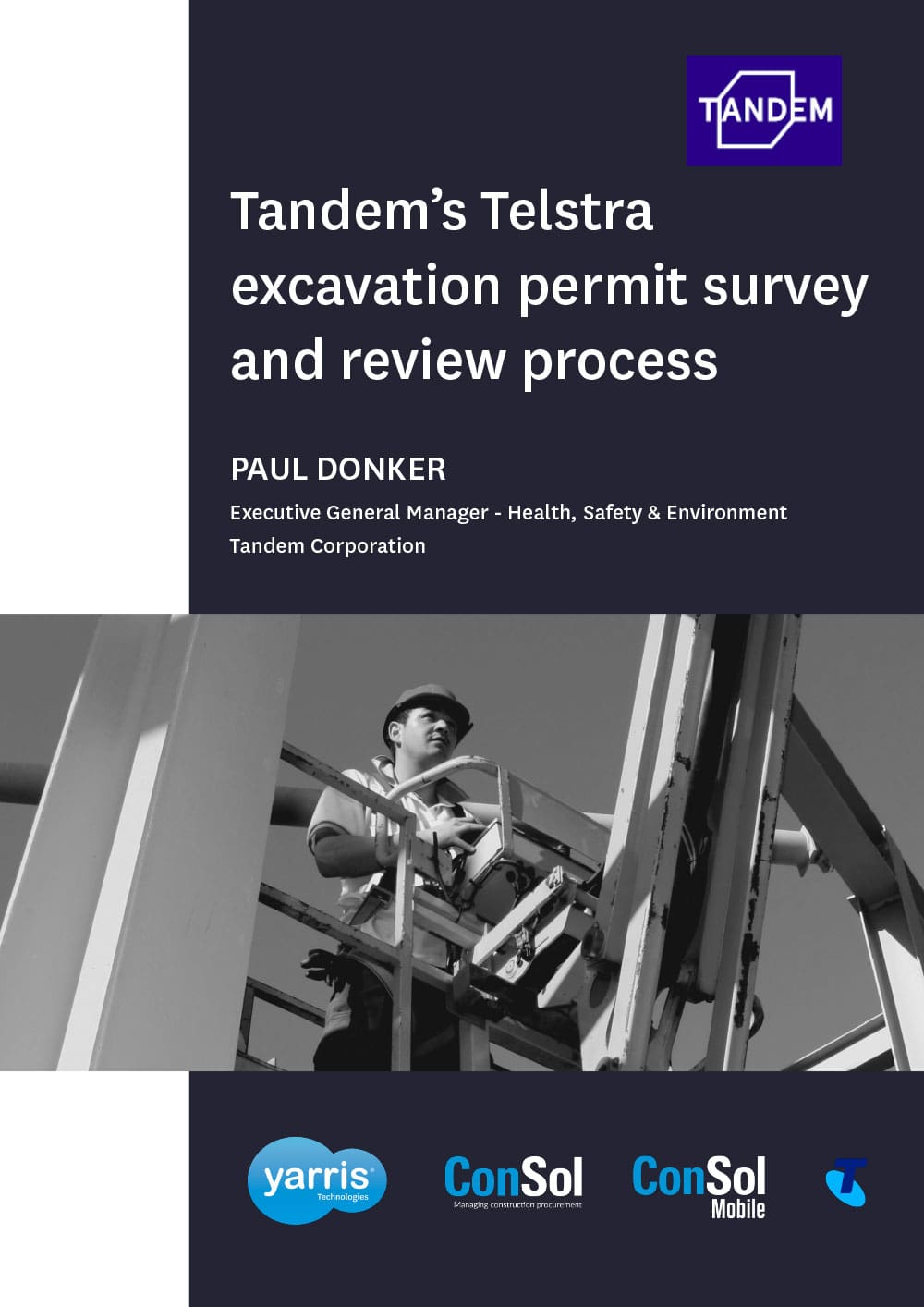
Tandem’s Telstra excavation permit survey and review process
Paul Donker
Executive General Manager – Health, Safety & Environment
Tandem Corporation
The role
I’m the Executive General Manager for Health, Safety and Environment for the Tandem group of companies, where we manage installation and maintenance, medium construction and civil construction. I’ve been at Tandem for about seven years, and prior to that I had a background with a number of other large organisations, including NBN. So, telco is a large part of my career.
My portfolio is essentially health, safety and environment and the quality of our management systems across Tandem, from strategic direction through to risk management, and then our assurance programs including field based monitoring to make sure that those systems are effective across the Tandem group of companies.
The role of technology
Technology enables us to embed business rules, requirements, standards and processes into our system which then forces those outcomes to happen. Technology is an enabler of assurance. Without actually having to get to a site, we can use technology to increase our scope and coverage of those assurance activities without actually having to throw additional resources at it. The technology captures real time artefacts and then enables us to remotely validate those artefacts.
The field services applications we use, capture detailed artefact information to enable trend analysis, identifying issues before they arise. Part of our strategic direction is to continue to leverage systems to use more remote monitoring capability, so we can increase monitoring validation in real time. Technology embeds the business rules that we need and supports people to follow a process.
Technology drives efficiencies
Efficiency means doing more with less, so rather than sending a person to manage an assurance activity at a site, I can do more using technology to do that for us, and by building business rules into the technology, so you can’t start the next part of the process until you collect the relevant artefacts. The system either interrogates or checks progress. Or it’s checked remotely. I don’t need to send a person to a site, I can have a person remotely check the submitted activities. We can just get people to go ahead to do those tasks, doing much more with less.
The business problem
We implemented a best-practice process based on our safety requirements. The challenge was to build a process that has two validation points. First, a validation of the underground assets and whether the planned excavation is deemed either low, high or extreme risk. We check what assets are in the ground and then based on that, determine what permit needs to be completed at site. We engage a team to check or validate that we’ve made the right determination about what needs to happen at the site.
For the second validation point where we have identified high or extreme risk assets we will need to work near, we have an on-site review involving a team member to make sure the civil crews are completing the task in adherence with all safety processes.
We’re focusing on the first validation point now, making the right determination. So, you can’t move to the next stage until the system and the business rules within the system are approving this first stage or this first validation point.
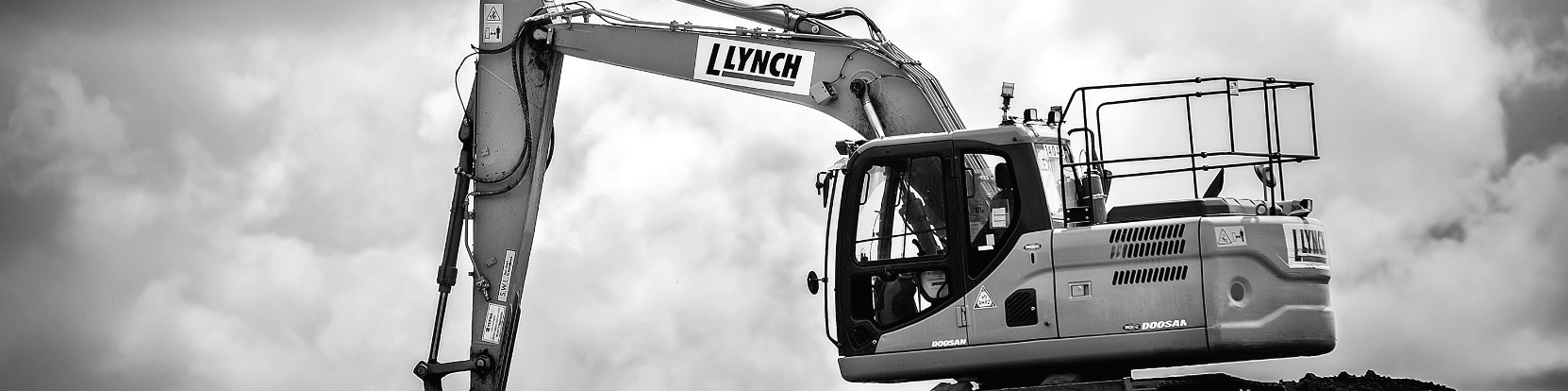
Safety as a client directive
We put a process in place at the request of our clients to manage their construction. Once we implemented it and looked at it over one or two months, we identified an opportunity to use a system change to provide process assurance. The customer requested a system change, or a change in the process, to provide a hold point. The purpose of the hold point was to prevent the work from happening in the field until a validation of that hold point has been completed. And I would see that as absolute best business practice. It’s probably going a bit above and beyond. Many organisations rely on people to do the right thing. This essentially takes that decision-making process away and makes sure that work in the field cannot even commence until this additional safety check has happened.
The challenges to address now
We have a number of stakeholders in the process , including clients, Tandem, and Tandem subcontractors. The challenge was to deliver an automated system that reduced effort, created a single point of truth, prevented field work from commencing without safety checks occurring, with all these automated and monitored from a system/field perspective, using system enforced hold points.
Implementing the change
Our project planning was well organised with weekly meetings and updates. From experience, I’ve always said that having dealt with a number of IT solutions over my career, you’ve usually got to double the time and double the cost. In this case we actually stuck to the timelines. and the cost was almost unchanged. So, that’s a really good outcome for Tandem and for Yarris, who scoped the system build well and held to the agreed project plan.
The weekly meetings involved a large stakeholder audience, including Telstra, operational management, heath and safety and, work deployment (very much part of the process) and those how were interacting with our sub-contractors to get feedback also.
It was good to open it up to a wider project team to gain input from all stakeholders. Where issues arose, we received feedback quickly about whether we could accept it or not, or suggest slight modifications to the plan. I saw a really quick response from Yarris on that one. And there was good feedback from Yarris – in real time.
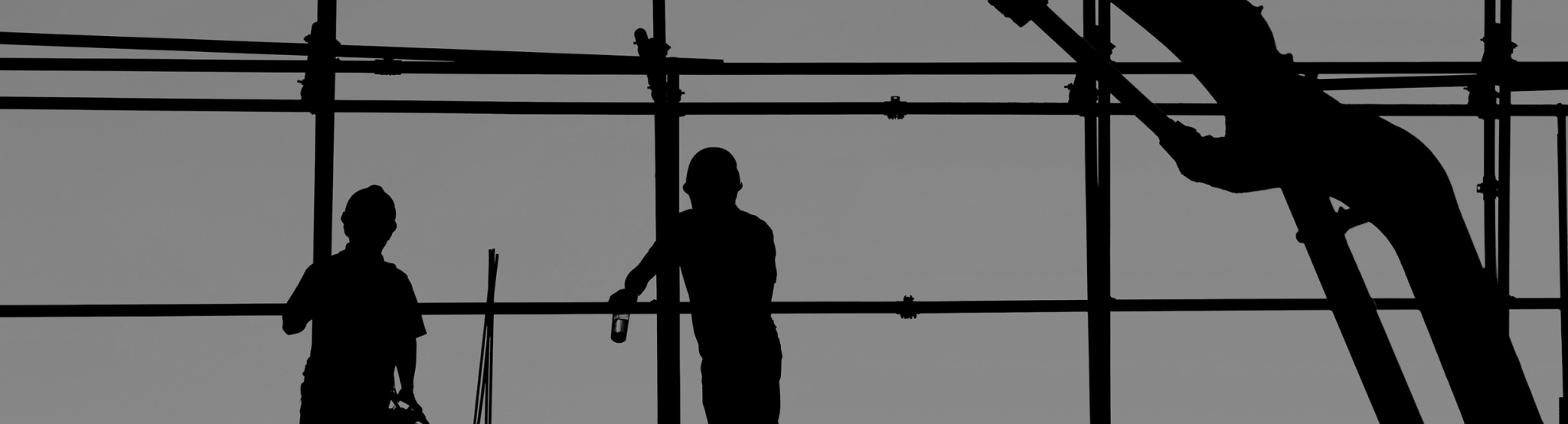
The outcomes
When we submitted the scope, it was quite open. Essentially, ConSol had some of the functionality we required and process support we were trying to achieve. I actually liked the way that the ConSol team designed the solution, using as much existing functionality within the system as possible, so they weren’t recreating the system. As the workshops developed, and as we met, week after week, developing the simplicity in the screens together was really good.
There’s an incredible amount that happens behind the scenes. And when I looked at the process, that actually, to me, was a very simple process, create this hold point one, require the subcontractors, to do this, tick this box, tick that box. Yarris made it simple in and intuitive for users , a good outcome for the people using the system.
Our users know they need to tick this box or upload this document, they don’t need to know what sits in the back end about all the business rules working behind the scenes. It means if they do the wrong thing, it won’t let them get to the next state. That’s what the ConSol team brought – simplicity from a user perspective. So, all those business rules that are happening in the back end, which we sorted out through a lot of questions, you’ve taken all that work, and made an appealing system – really simple and intuitive. It was great that the feedback from subcontractors around the user acceptance testing confirmed that it was going to reduce their admin time.
Subcontractors could instantly see the benefits of using this system, rather than a manual process relying on emails, which may get lost. This automates the process and gets rid of all that lost data. Putting an end to re-keying the same data twice. With the data already in the system, they see or reuse it. . There are dropdown boxes to speed up their process. Great to see that initial feedback from them.
What’s next?
For our hold point functionality we created a very detailed process flow from an end-to-end perspective of excavation works and having a low, high or extreme risk permit approved. Hold point one is the risk assessment of which permit needs to occur.
And then we’ve got hold point two, which we’ll look at next with another project to capture video and artefacts from hold point two and automate these back into ConSol. We’ll see if we can create some system smarts within ConSol, that can help us with hold point two.
We also want to tackle multiple-channel video calls, where we have to call in a number of different stakeholders to approve that permit on site. So, whether we go to site or not, we’ve still got a process where we have to have video/photos records so there’s a good artifact evidence.
I think there’s still an opportunity to further automate some of these processes within ConSol to further improve the system to ensure greater efficiency and assurance. I hope we can collaborate on that once we wrap this one up.